Capabilities
TYGOR Laboratories performs metallurgical non-destructive testing, primarily for the helicopter manufacturing and overhaul industry. Non-destructive testing refers to a wide range of inspection methods whose purposes are to reveal flaws in parts or materials that are not readily visible to the un-aided eye. These methods do not alter or damage the article under test. Specifically, TYGOR performs the magnetic particle and fluorescent dye penetrant inspection methods.
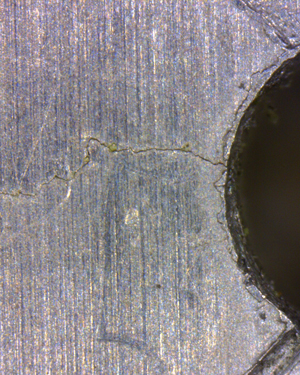
Magnetic Particle Inspection (MPI)
This inspection method is designed to detect surface, and moderately sub-surface, flaws in ferrous metals such as various grades of steel. By bathing the test article in magnetic particles and creating a magnetic field within the test article, the particles attach to any defects thus making them apparent to the trained eye.
TYGOR’s magnetic particle inspection department features 3 Wet Horizontal DC Magnaflux® machines with output to 6000 amps all configured for fluorescent inspection. These machines are capable of handling parts up to 100 inches in length. For parts greater than 100 inches in length, or unique project requirements, the department is capable of performing the Wet or Dry Particle method using portable equipment. Following inspection, all parts are demagnetized and cleaned of particles. Where requested by the customer parts can be post-preserved to prevent corrosion.
Fluorescent Penetrant Inspection (FPI)
This inspection method is designed to detect flaws open to the surface mainly in non-ferrous materials such as aluminum, magnesium and titanium. The test article is coated with fluid specifically designed to penetrate tight, surface defects by way of capillary action. Following a specific duration of time the test article is washed of excess penetrant leaving behind only the fluid caught in defects thus making them apparent to the trained eye.
TYGOR’s fluorescent penetrant department features two stationary Zyglo® machines employing High Sensitivity penetrant materials. These machines are capable of handling parts up to several feet in length. For unique project requirements the department also has a variety of portable Zyglo® equipment.
Equipment & Materials
TYGOR uses Magnaflux® and Zyglo® equipment and materials exclusively. All our consumable materials have traceability back to the manufacturer’s original processing. All our machines are calibrated with N.I.S.T. traceability. No piece of equipment in our lab is exempt from calibration. We perform and record daily, weekly, monthly, quarterly and semi-annual performance checks in addition to independent onsite, third party calibrations.
Part Size / Geometry / Quantity
TYGOR Labs is capable of processing a very wide variety of items. We can inspect parts that range in size from fractions-of-an-inch up to several feet long. Part geometries can range from fairly simple lock-pins to welded frame assemblies to very complex cast gearbox housings. Part quantities can range anywhere from one-off items to volumes in the tens-of-thousands.
If you have a specific project you’d like us to review with you, please contact us.